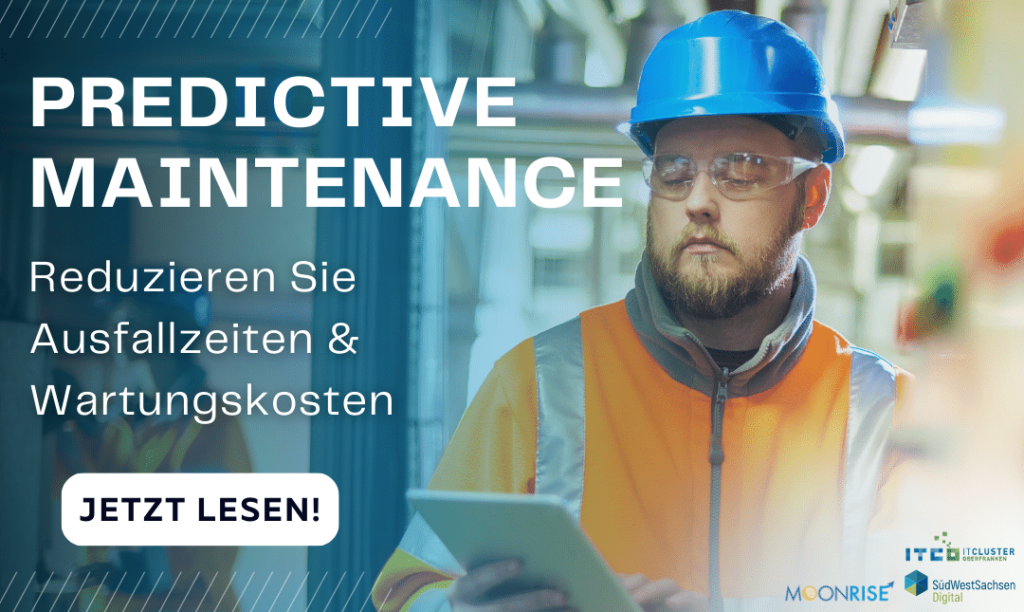
Predictive Maintenance – Definition, Anwendung & Beispiele aus der Praxis
Predictive Maintenance, oder vorausschauende Instandhaltung, ist ein entscheidender Faktor für effiziente und kosteneffektive Produktionsprozesse. Mit dem Einsatz moderner Technologien und umfangreicher Datensammlungen ermöglicht Predictive Maintenance die Reduzierung von Ausfällen, die Vorhersage von Wartungsbedarf und die Optimierung der Produktionsabläufe. In diesem Artikel werden wir die Anwendungsmöglichkeiten von Predictive Maintenance genauer anschauen und anhand von zwei Beispielen aus der Praxis demonstrieren, wie es erfolgreich implementiert werden kann. Los geht’s!
Definition Predictive Maintenance: Was ist vorausschauende Instandhaltung?
Predictive Maintenance, auch prädiktive oder vorausschauende Instandhaltung genannt, bezeichnet einen Wartungsvorgang, welcher auf Auswertungen von Prozess- und Maschinendaten basiert. Der Begriff Predictive Maintenance findet sich vor allem im Kontext der Industrie 4.0 wieder. Durch die Auswertung von Daten in Echtzeit, macht Predictive Maintenance Prognosen möglich, die eine bedarfsgerechte Wartung von Maschinen o.Ä. ermöglichen und dadurch Ausfallzeiten effektiv reduzieren können. So können wirtschaftliche Ziele schneller und effektiver erreicht werden.
Durch den Einsatz von Predictive Maintenance kann der Zustand von im Betrieb befindlichen Maschinen und Geräten bestimmt werden, um so zu bestimmen, wann eine Wartung durchgeführt werden sollte. Somit werden Wartungen nur noch dann ausgeführt, wenn sie auch wirklich notwendig sind und beugen dem Ausfall von Maschinen und Geräten vor. Gegenüber routinemäßigen oder zeitabhängigen vorbeugenden Warten können damit Kosteneinsparungen erzielt werden. Das Hauptziel von Predictive Maintenance ist damit die möglichst präzise Vorausplanung der Instandhaltung und die damit verbundene Vermeidung von Ausfällen.
Möglichkeiten & Anwendung von Predictive Maintenance
(Predictive) Maintenance spielt, laut Frank Baumann von der Firma DURAMENTUM GmbH, für jede Firma, die irgendetwas herstellt, eine entscheidende Rolle. Dabei ist egal, was hergestellt wird. Betrachtet man Anlagen oder Maschinen, so ist es für den Betreiber dieser Anlagen oder Maschinen immer das Ziel, diese bestmöglich zu nutzen. Gemessen wird dies an der internationalen Kenngröße OEE (Overall Equipment Effectiveness = Gesamtanlageneffektivität). Die entscheidenden Unterfaktoren sind hierbei: Verfügbarkeit, Leistung und Qualität.
Der Einsatz von Predictive Maintenance hat einen unmittelbaren (positiven) Einfluss auf die Unterfaktoren:
- Verfügbarkeit: Läuft die Maschine ohne Probleme?
- Qualität: Produziert die Maschine, die Produkte in der Qualität, die der Kunde erwartet?
Diese Faktoren gilt es durch den Einsatz von Predictive Maintenance auf dem höchstmöglichen Niveau zu halten oder dort hinzubringen. Dabei spielt wiederum auch der Mensch eine entscheidende Rolle, da dieser zum richtigen Zeitpunkt an der richtigen Maschine Wartungsarbeiten oder Reparaturen durchführen muss.
Daten als Grundlage für Predictive Maintenance
Predictive Maintenance basiert auf Daten und nutzt bestimmte Wahrscheinlichkeitsmodelle, um Vorhersagen zu treffen. Damit bilden Daten die essenzielle Grundlage für den effektiven Einsatz von Predictive Maintenance und der Umfang der Daten sowie die Qualität der Daten sind entscheidende Faktoren für die Effektivität und Präzision.
Um das Thema anzugehen, ist daher die entsprechende Sensorik an der Maschine Voraussetzung, die bestimmte Daten sammeln kann. Zudem ist eine möglichst große Historie an Daten von Vorteil, welche genutzt werden können. Baumann betont, dass trotz all der Technologie weiterhin das Wissen der Handwerker ein unerlässlicher Faktor, für die Effektivität von Predictive Maintenance ist.
Die Rolle von Vorhersagbarkeit und Ausfallreduzierung
Das Ziel von Predictive Maintenance ist, wie bereits beschrieben, zum einen die Reduzierung von Ausfällen und zum anderen die Vorhersagbarkeit von Problemen mit der Maschine zu ungünstigen Zeitpunkten, zu denen ggf. Entscheidungsträger oder entsprechende Mitarbeiter nicht verfügbar sind. Die Vorhersagbarkeit ist laut Baumann damit in vielen Fällen wichtiger als die pure Reduzierung von Stillständen.
Der Faktor Mensch: Wieso nach der Analyse noch nicht Schluss sein darf
Wie Frank Baumann, betont auch Jonas Szalanczi von NeuroForge, dass der Faktor Mensch beim Einsatz von Predictive Maintenance von hoher Wichtigkeit ist. Er spricht dabei von drei verschiedenen Ebenen beim Predictive Maintenance:
Ebene 1 – Maschinenebene: Die Maschine übermittelt ihre Sensorwerte
Ebene 2 – Datenlayer: Die Daten der Maschine werden im Data Warehouse aufgenommen, gespeichert und in Echtzeit analysiert
Ebene 3 – Nutzerebene: Die verarbeiteten Daten werden für den Endnutzer aufbereitet und die Signale entsprechend dargestellt
Gerade für die Führungsebene sind Reportings und die entsprechende Speicherung der Daten entscheidend. Zudem sollte beim Auftreten eines Fehlers oder einer Störung automatisch ein Techniker kontaktiert werden, um die Ausfallzeit so gering wie möglich zu halten. Denn jetzt kommt wieder der Mensch ins Spiel. Auch das Lösen des Problems sollte im System festgehalten werden, damit vollkommene Transparenz und Nachvollziehbarkeit gewährleistet ist und der Faktor Mensch berücksichtigt wird.
Predictive Maintenance – Beispiel in der Kunststoffverarbeitung
In unserem ersten Predictive Maintenance Beispiel geht es um den Bereich Kunststoffverarbeitung. Felix Franke von der d-opt GmbH berichtet von einem mittelständischen Unternehmen aus der Luft- und Raumfahrtherstellung sowie Automobilzulieferung, welches fünf Spritzgussmaschinen gleichen Typs und drei größere Maschinen im Einsatz hat. In diesem Bereich werden recht hohe Stückzahlen produziert.
Bei der Kunststoffverarbeitung ergeben sich folgende Herausforderungen:
Verfügbarkeit der Maschinen: Die Anlagen sind recht teuer und es muss durchgehen produziert werden, um den entsprechen Gewinn sowie Rückfluss erreichen zu können.
Aufwendige Instandhaltung: Wenn Dinge an den Maschinen kaputtgehen, sind es in der Regel recht kostenintensive Teile, die ersetzt werden müssen und der Personalaufwand ist sehr hoch.
Geringe Personalkapazität: Das Beispielunternehmen hat ein hybrides Instandhaltungsteam, bestehend aus drei Mitarbeitern am Standort selbst und einem zusätzlichen Instandhaltungsdienstleister. Alles, was sich schnell lösen lässt, wird von den eigenen Mitarbeitern bearbeitet und aufwendigere Themen werden durch den Dienstleister behoben.
Schwierige Ersatzteilbeschaffung: Im Bereich der Kunststoffverarbeitung sind die Ersatzteile für die Maschinen nur schwer zu bekommen und häufig mit mehreren Monaten Lieferdauer verbunden. Zudem sind die Bauteile oft individualisiert.
Der Einsatz von Predictive Maintenance unterstützt hierbei effektiv die Reduktion von Ausfällen der Anlagen und Maschinen und sichert zudem eine Vorhersehbarkeit, sodass die genannten Herausforderungen möglichst einfach bewältigt werden können.
Die verfügbare Datenbasis
Wie bereits erläutert, braucht es für Predictive Maintenance eine gewisse Datenbasis, welche möglichst umfangreich und gut in der Qualität ist. Ausgehen von dem Beispielunternehmen in der Kunststoffverarbeitung lagen Excel-Listen mit Daten zu bisherigen Ausfällen und Reparaturen vor, welche hervorragend gepflegt wurden. Es wurde festgehalten:
- Wann ein Ausfall aufgetreten ist
- Um welche Art von Ausfall es sich handelte
- Die dazugehörigen Reparaturmaßnahmen
- Wer die Reparatur durchgeführt hat
- Der Grund für den Ausfall
Die vorhandenen Maschinen im Unternehmen sind zum Teil netzwerkfähig und seit mehreren Jahren ins System eingebunden. Von den fünf Anlagen neueren Typs sind drei netzwerkfähig. So wird schon eine Vielzahl an Parametern gespeichert. Um auch alle Maschinen überwachen zu können, wurden zusätzlich die Energie, Temperatur und Schwingungsdaten erfasst.
Predictive Maintenance als Lösung
Die verfügbare Datenbasis kann nun genutzt werden, um Predictive Maintenance im Unternehmen zu implementieren. Wichtig ist es, die Datenbasis um Prozesswissen von Experten zu erweitern, welche sich mit den Funktionsweisen und der Instandhaltung sowie Reparatur der Maschinen auskennen. Das Prozesswissen wird in Interviews erfasst und expliziert und dient dann gemeinsam mit der Datenbasis als Ausgangspunkt für das KI-Modell zur Analyse und Bewertung der Maschinen.
Mithilfe der KI-Modelle für das Predictive Maintenance kann nun der aktuelle Zustand der Maschinen dargestellt werden. So wird ersichtlich, in welchem Zustand sich die jeweilige Maschine befindet und mit welcher Erwartung diese eingesetzt werden kann.
Zudem können mithilfe von Predictive Maintenance in einem Dashboard Prognosen und Risikolevels für die jeweiligen Maschinen und Anlagen bereitgestellt werden. So kann anhand der vorhandenen Daten eingeschätzt werden:
- wie sich die Maschine in Zukunft entwickeln wird und
- ob es bestimmte Bauteile gibt, die gefährdet sind.
All diese Informationen werden für das Beispielunternehmen in einer App in einem einfachen Ampelsystem dargestellt, sodass jeder Mitarbeiter in der Lage ist, den Zustand der Maschinen zu überprüfen.
Predictive Maintenance – Beispiel bei VW
In unserem zweiten Beispiel geht es um den Einsatz von Predictive Maintenance im VW Motorenwerk Chemnitz. Im VW Motorenwerk Chemnitz werden Benziner- und Dieselmotoren gefertigt. Dr. Matthias Nagel von Simba n3 erklärt, dass die besondere Herausforderung dabei ist, dass Ersatzteile häufig mit dem Hubschrauber eingeflogen werden müssen, damit die Produktion nicht ausfällt und zudem mehrere Tausend Maschinen überwacht werden müssen.
Zudem ist gerade bei einem Unternehmen wie dem VW Motorenwerk Chemnitz wichtig, dass nicht nur die einzelnen Maschinen und Anlagen überwacht und instandgehalten werden, sondern ganze Produktionslinien kontrolliert werden. Allein für einen Zylinderkopf werden in der Fabrik bis zu 15 Maschinen benötigt, die alle überwacht werden müssen.
Störcodes und Serviceberichte als optimale Datenquellen für Predictive Maintenance
Wie auch schon im vorangegangenen Beispiel aus der Praxis deutlich wurde, ist die Datenbasis entscheidend für eine effektive Implementierung von Predictive Maintenance in der Produktion. Bei VW gibt es spezielle Störcodes und Serviceberichte, die vollständige Informationen zu den Ereignissen und der Regulierung von Störungen enthalten. Diese Daten sind bei VW alle digital verfügbar. Zudem liegen diese Serviceberichte allen Maschinenbetreibern und / oder Reparaturdienstleistern vor. Die Daten aus den Serviceberichten lassen optimalerweise auch die Ermittlung des Verbrauchs der Maschine oder einzelnen Komponenten bis zur Reparatur zu.
Weitere Vorteile von der Arbeit mit Ereigniszeit-Daten (Serviceberichten):
- Ereigniszeitmodelle kommen mit nur wenigen Daten aus
- Die Ergebnisse haben eine hohe Transparenz und sind gut erklärbar
Ausfallvorhersage mit Wahrscheinlichkeitsmodellen
Aus den Ereigniszeit-Daten lassen sich optimal Wahrscheinlichkeitsmodelle ableiten, die eine Ausfallvorhersage für verschiedene Maschinen, Komponenten und Störungsursachen herleiten. So ermöglicht Predictive Maintenance auch, dass verschiedene Szenarien simuliert werden können, um zu sehen, wie sich verschiedene Faktoren und Komponenten auf die Laufzeit, Effektivität und Funktionsfähigkeit einer Produktionslinie auswirken. Die Wahrscheinlichkeitsmodelle berücksichtigen also verschiedene Ereignisse & ungestörte Prozesse.
Dadurch, dass bei diesem Praxisbeispiel bei VW mit Wahrscheinlichkeitsmodellen gearbeitet wird, sind die verschiedenen Maschinen vergleichbar. Diese Vergleichbarkeit lässt wiederum Wahrscheinlichkeitsaussagen für ganze Produktionslinien zu. Zusätzlich ermöglichen die empirischen Daten Strategie-getriebene Erhaltung und ökonomische Kosten-Nutzung- Abschätzungen.
Seit 2018 ist Predictive Maintenance über Wahrscheinlichkeitsmodelle beim VM Motorenwerk Chemnitz im operativen Einsatz und wurde bereits als voller Erfolg gewertet. In einem Dashboard sind die einzelnen Produktionslinien mit allen laufenden Maschinen der Linie einsehbar und die Ausfallwahrscheinlichkeit zwischen 0 und 1 zeigt an, ob eine Maschine gewartet oder repariert werden muss.
Fazit: Predictive Maintenance für mehr Effizienz und Wirtschaftlichkeit
Predictive Maintenance hat das Potenzial, die Effizienz und Wirtschaftlichkeit von Produktionsprozessen erheblich zu steigern. Durch den gezielten Einsatz von Sensoren, Datenanalysen und künstlicher Intelligenz ermöglicht es Unternehmen, Wartungsarbeiten an den Maschinen frühzeitig durchzuführen, wodurch Ausfälle minimiert und Kosten gesenkt werden. Die Beispiele aus der Kunststoffverarbeitung und dem VW Motorenwerk Chemnitz zeigen, dass Predictive Maintenance bei der richtigen Umsetzung eine entscheidende Rolle für den Erfolg eines Unternehmens spielen kann.
Dennoch ist es wichtig zu betonen, dass der Mensch nach wie vor eine zentrale Rolle bei der erfolgreichen Implementierung von Predictive Maintenance spielt. Erfahrene Fachkräfte sind erforderlich, um Prozesswissen zu liefern, auf unerwartete Probleme zu reagieren und die gewonnenen Daten effektiv zu nutzen. In diesem Sinne ist Predictive Maintenance kein Ersatz für menschliche Expertise, sondern vielmehr eine Ergänzung, die das Potenzial hat, die industrielle Produktion nachhaltig zu optimieren und zukunftssicher zu gestalten.